Hardwood Panel Manufacturer
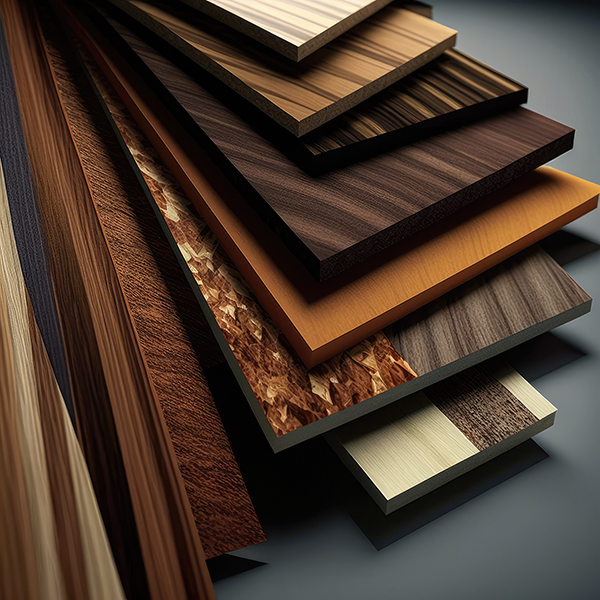
Scenario: The client, a composite and veneer core, hardwood veneer, construction, cabinet and furniture panel manufacturer with 5-sites nationally and ~$115 mil. in annual revenue. My role was to lead and organization-wide lean implementation introducing Kaizen, 5S, total productive maintenance, single-piece flow, poke-yoke, visual communication an set-up time reduction across the company.
In executing this project, I followed a structured approach made up of the following phases:
Phase 1: Conducted a baseline assessment of the existing manufacturing processes, identifying the gaps and areas of improvement.
Phase 2: I designed and developed a comprehensive Lean transformation roadmap, detailing the project scope, timeline, deliverables, and success metrics.
Phase 3: With functional areas partners I created a project management plan, outlining the roles, responsibilities, and accountabilities of all project stakeholders.
Phase 4: With project stakeholders assistance I formed and trained a dedicated Lean implementation team, comprised of cross-functional resources from across the organization.
Phase 5: I facilitated Kaizen workshops, involving all relevant stakeholders, to identify opportunities for improvement in manufacturing processes, workflows, and workstations.
Phase 6: With functional team participationg we implemented 5S methodologies focused on improving the organization and cleanliness of the workplace, optimizing productivity, efficiency, and safety.
Phase 7: I facilitated the establishment of a Total Productive Maintenance (TPM) practice optimizing equipment availability, performance, and reliability.
Phase 8: I introduced and facilitated the practice of single-piece flow, poke-yoke, and set-up time reduction techniques that led to optimizing the production processes and waste elimination.
Phase 9: I implemented visual communication practices to improve communication across the organization, making it easier for stakeholders to more quickly understand and act upon critical information.
Phase 10: Throughout and post project I conducted regular reviews of the Lean implementation project, monitoring the progress, performance, and impact of the project, and initiating corrective action(s) as required.
Metrics:
- Manufacturing throughput rate reduction from 5-7 days to 3-5 days
- 10% reduction in work-in-progress (WIP) inventory, resulting in a $1.2 million reduction in costs.
- $1.4 million reduction in finished goods inventory
- Increased employee engagement and satisfaction, as measured through employee surveys and retention rates.
Future State: Future initiatives that could be pursued to further improve the organization's operations include: The introduction of Industry 4.0 technologies such as smart manufacturing, predictive maintenance, and advanced data analytics to improve process efficiency and productivity. The introduction of AI supported improvement activities such as: reducing and automating workload, employee training and effectiveness, complex project management, natural language processing and prompts and data analysis and optimization. The expansion of Lean practices to other areas of the organization, such as procurement, logistics, and customer service, to further optimize the value chain. Establishing a continuous improvement culture, encouraging ongoing process improvement and employee engagement in driving operational excellence.
Outcome: I led an organization-wide Lean implementation project at a composite and veneer core, hardwood veneer, construction, cabinet and furniture panel manufacturer. Through this I introduced Kaizen, 5S, total productive maintenance, single-piece flow, poke-yoke, visual communication an set-up time reduction practices. Overall, this resulted in improved manufacturing throughput rates, reductions to WIP and finished goods inventory, and increased employee engagement and satisfaction. This project established a solid foundation for future initiatives such as Industry 4.0 adoption, AI process augmentation and the embracing of a continuous improvement culture.