JIT Digital Book Printing and Fulfillment
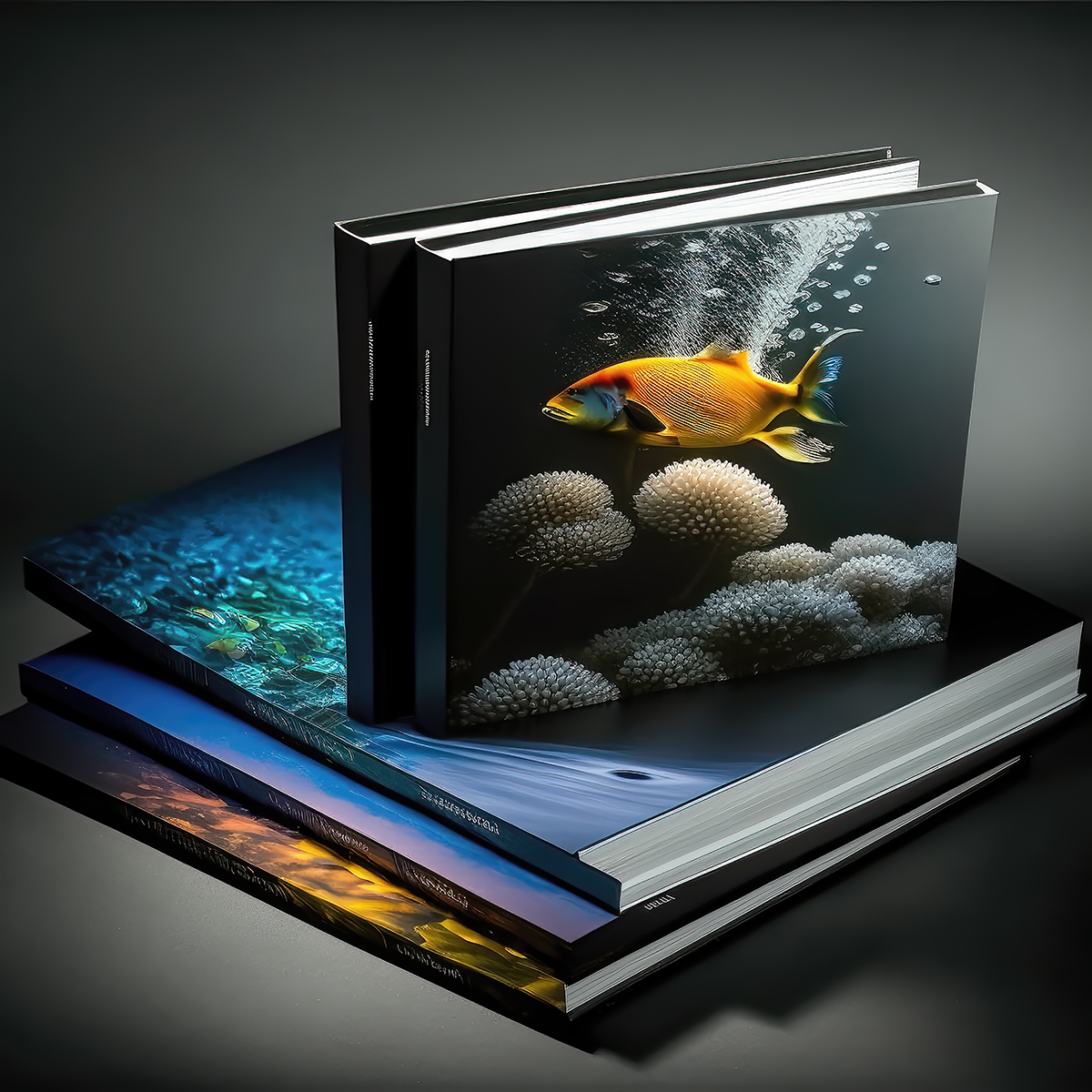
Scenario: The client, a digital photo book manufacturer with their primary product being digital photo books supplemented by calendars, notecards and stickers; generating $27 million in revenue. The client needed to rapidly expand their facility output and manufacturing equipment count to increase their capacity and efficiency. The client also needed to convert to a single-piece flow configuration to better mirror customer order sequencing and reduce process bottlenecks. All of this work had to be accomplished without impacting their 20/7 operating schedule and 48-hour turn on customer order fulfillment.
To address these needs, the project was executed in several phases over a six-month timeframe.
Phase 1: Facility Expansion and Equipment Installation In this phase, the client needed to increase their facility size by 50% to accommodate the additional equipment required to meet their expansion goals. This task involved locating and leasing space that met their requirements, resolving permitting and electrical/internet service roadblocks, and executing the facility build-out and equipment installation/commissioning. The team successfully installed four high-speed digital printers and twelve wide-format inkjet printers, which significantly increased the client's manufacturing capacity.
Phase 2: Single-Piece Flow Conversion In this phase, the team converted the client's manufacturing process from small batch (15-20) orders to single-piece flow. The team worked with the client to develop and train new practices that would enable them to switch from small batch to single-piece flow. The team also re-laid out the facility/flow and installed material handling equipment that would enable the client to move quickly and efficiently through the new process.
Phase 3: Process Improvement Execution In this phase, the team executed process improvements that aimed to reduce key bottlenecks in the client's manufacturing process. The team reduced the key bottleneck from a 3-4-week training lead time to just two days to achieve the same proficiency level. This was done through a combination of training and process improvement, which reduced training times and increased overall proficiency.
Phase 4: Meeting Annual Holiday Demand The final phase of the project involved successfully meeting the annual ~8x holiday demand increase from October to December with a corresponding 5x increase in workforce. The improvements in facility size, manufacturing equipment, and single-piece flow conversion allowed for a more streamlined production process. This, combined with the process improvement execution, enabled the client to meet seasonal demands while improving the quality of their products.
Metrics:
- 50% increase in operational sqft. via acquisition and build-out of a 2nd facility
- 4 high-speed digital printers and 12 wide-format inkjet printers installed
- Switch from small batch to single-piece flow
- Key bottleneck reduced from a 3-4-week training lead time to just two days
- Successfully met the annual ~8x holiday demand increase from October to December with a corresponding 5x increase in workforce
Future State: Areas that the client may want to consider for improvement include exploring automation and machine learning to further optimize their manufacturing processes, implementing more advanced inventory management systems to improve forecasting and reduce waste, and exploring new product lines to diversify their revenue streams.
Outcome: The client was able to significantly increase their manufacturing capacity and efficiency while maintaining their high level of customer service. The improvements made through this project will allow the client to meet future demands and scale their business while enabling them to meet seasonal demands while improving the quality of their products.